11.
Why is the anti-blocking performance of control valves with straight strokes poor, while that of the rotary motion valve is good?
Valve spools of straight strokes throttle vertically, and the medium comes in and out horizontally. The flow path in the valve cavity will inevitably turn, which makes the flow path of the valve quite complicated (like a shape of horizontal "S"). In this way, there are many dead zones, which provide space for the precipitation of the medium. If things go on like this, it will cause blockage.
The direction of the throttling of the rotary motion valve is the horizontal direction. The inflow and outflow of the media are horizontal. It is easy to take away the dirty medium. At the same time, the flow path is simple and the medium is deposited with little space. Therefore, the rotary motion valve has good anti-blocking performance.
12.
What kind of circumstance do we need to use valve positioners?
(1) Valve positioners are used for places with great friction and where the positioning is required, for example, high temperature and low temperature control valves or control valves with flexible graphite packing.
(2)Valve positioners are required in the place where the response speed of the control valve needs to be increased in the slow process. For example, the adjustment system of temperatures, liquid levels, analyses, and other parameters.
(3)Valve positioners are applied in conditions where it is necessary to increase the output force and cutting force of the actuator, such as single-seat valves with a DN greater than or equal to 25 and double-seat valves with a DN greater than 100. The pressure drop at both ends of the valve △P is greater than 1MPa or the inlet pressure P1 10MPa.
(4) Valve positioners are needed in conditions that opening or closing by gas needs to be changed when the split-range regulating system and regulating valve are in operation sometimes.
(5) Valve positioners are applied to places where it is necessary to change the flow characteristics of the regulating valve.
13.
What are the seven steps to determine the size of the regulating valve?
(1) Determine and calculate flow rates: Qmax or Qmin.
(2) Determine and calculate pressure difference. Select the value of the resistance ratio S according to the characteristics of the system, and then determine and calculate the fully opened
valve.
(3) Pressure difference
(4) Calculate the flow coefficient. Select the appropriate calculation formula chart or software to get the max and min of KV.
(5) Select the KV value. Select the KV value that is closest in the selected product series according to the KV max value. The primary diameter is obtained.
(6) Checking computations of the opening angle: when Qmax is required, the opening angle of valves should not be greater than 90%; when Qmin is needed, the opening angle of valves should not be smaller than 10%.
(7) Checking calculation of actual adjustable ratio: the general requirement should not be smaller than 10; the actual R should be greater than the required R.
(8) Determination of the diameter: if it is unqualified, reselect the KV value and verify again.
14.
Why can't the sleeve valve replace the single-seat and double-seat valves?
The sleeve valve that came out in the 1960s was widely used at home and abroad in the 1970s. The sleeve valves of the petrochemical plants introduced in the 1980s accounted for a large proportion. At that time, many people believed that sleeve valves could replace single and double seat valves, becoming the second-generation product. Until now, that is not the case. Single-seat valves, double-seat valves, and sleeve valves are used together. This is because only the throttling form, stability and maintenance of the sleeve valve are improved, but its weight, anti-blocking, and leakage indicators are consistent with the single and double seat valves. How can it replace the single and double seat valves? Therefore, they can only be used together.
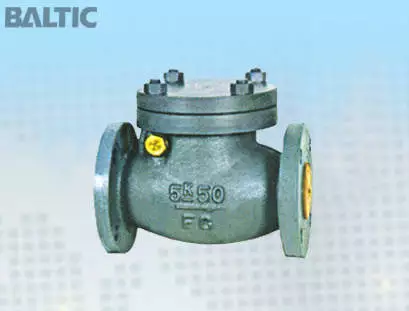
15.
Why should hard seals be used as far as possible for shut-off valves?
The shut-off valve requires that the leakage is as low as possible. The leakage of the soft-sealed valve is the lowest. The shut-off effect is certainly good, but it is not wear-resistant and has poor reliability. Judging from the double standards of small leakages and reliable sealing, soft-sealing is not as good as hard sealing. For example, an ultralight regulating valve with full functions is sealed and protected with wear-resistant alloys, which has good reliability, a leakage rate of 10 to 7, and can already meet the requirements of a shut-off valve.
16.
Why is the stem of the straight-stroke control valve thinner?
It involves a simple mechanical principle: the greater the sliding friction is, the smaller the rolling friction becomes. The valve stem of the straight-stroke valve moves up and down. If the packing is slightly compressed, it will pack the valve stem very tightly, resulting in a big return difference. For this reason, the valve stem is designed to be very small, and PTFE packing with a small friction coefficient is often used for the packing to reduce return difference. However, there will be a problem with thin valve stems, which makes them easy to bend and have short service life for the packing. The best way to solve this problem is to use a rotary valve stem, that is, a control valve with angular travels. Its stem is 2 to 3 times thicker than that of a straight travel. Graphite packing with a long service life and stems with good rigidity should be selected. The friction torque is small and the return difference is small.